The LIFE PlasPLUS project brings together a university (The University of Liège), a research centre (CRF) and 3 industrial operators (Comet Traitements, SERI PLAST and Campine) from Belgium and Italy. Together we represent a consortium of highly experienced and well-recognized partners. Under the project coordination of Comet Traitements and with a €3.17 million budget, the LIFE PlasPLUS consortium will operate for 42 months and work together to provide the greatest possible solutions within the project scope of work.
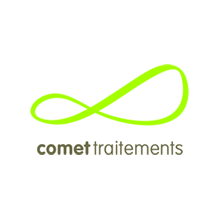
Comet Traitements / Project coordinator
Comet Traitements is a Belgian innovative high-growth company processing and recycling shredder residues, the by-product of the shredding of metallic wastes. Since its creation in 2002, they have developed and industrialised more than 8 post-shredder separation and recycling processes for the recovery of non-ferrous metals, minerals, iron oxides, synthetic fuel, plastics, etc. The success of these technologies has helped Comet Traitements to build up in Belgium sustainable supply chains of secondary raw materials, meet EU targets on recovery rates and secure its reputation as an industry leader.
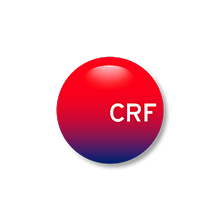
Centro Ricerche Fiat
The mission of Centro Ricerche Fiat, part of FCA (Fiat Chrysler Automobiles), lies in three main goals: i) to develop innovative power units, vehicle systems, materials, methods and processes to improve the competitiveness and sustainability of FCA products, ii) to represent FCA as part of European and national collaborative research, taking part in pre-competitive research projects and promoting the development of a network of contacts and partnerships on an international scale and iii) to support FCA in enhancing the value of its intangible capital.
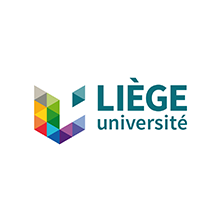
Université de Liège
The University of Liege was founded in 1817 and counts more than 25.000 students, including 5.000 foreign students from almost 130 nationalities. The GeMMe, a Research Unit specialized in georesources, mineral engineering and extractive metallurgy, derives its know-how from a long research tradition in primary ores mining and processing. The GeMMe actively contributes to the development of innovative processes for the efficient management of mineral and metallic resources while providing unparalleled upscaling experience in urban ore characterization and processing (with a focus on innovative sorting techniques and hydrometallurgy).
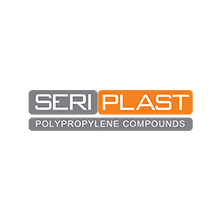
SERI PLAST
SERI PLAST is an innovative and flexible company that deals with the production of thermoplastic compounds mainly based on polypropylene and polyethylene (recovered from industrial scraps and virgin raw materials). The need to compete on the global market constantly encourage SERI PLAST to reach the highest standards, taking care and improving costs and efficiency of its production processes.
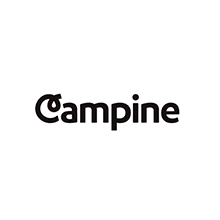
CAMPINE
Campine Specialty chemicals is active in the additive market for plastics, as a supplier of flame retardant masterbatches, and antimony trioxide (flame retardant synergist, but also used as catalyst in PET or as a pigment). Campine recycling is active in the supply of lead alloys for the battery industry but also for (radioactive) shielding, electric cable protection.